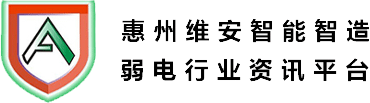
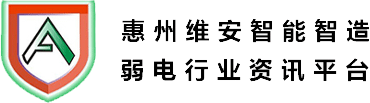
随着科技的发展和工业4.0时代的到来,智慧园区已成为推动制造业转型升级的重要载体。其中,智慧工厂通过引入先进的信息技术、物联网(IoT)和大数据分析等手段,实现了从传统生产模式向智能、高效、绿色生产方式的转变。预测性维护作为智慧工厂中的关键技术之一,不仅能够有效减少设备故障,还能显著提升生产效率和产品质量。本文将探讨惠州智慧园区中,智慧工厂是如何通过预测性维护实现这一目标的。
预测性维护是基于对设备运行状态的实时监控和数据分析,通过预测设备可能发生的故障或性能下降趋势,提前采取措施进行维修或更换零件,以避免意外停机和生产中断。这一过程通常涉及传感器收集设备运行数据、边缘计算处理数据、云平台存储和分析数据,以及决策系统生成维护建议等多个环节。
在惠州智慧园区的智慧工厂中,通过部署物联网传感器,收集设备的温度、振动、电流等关键参数,并将其传输至云端进行分析。利用机器学习算法,系统能够识别出设备的异常行为模式,预测潜在故障。同时,通过集成的决策支持系统,自动化生成维护任务,指导现场维护人员高效执行。
园区内的智慧工厂采用了全面的数据收集和分析策略。实时监控数据不仅帮助识别设备的早期故障迹象,还为持续改进提供依据。例如,通过对历史数据的分析,可以优化设备的运行参数,延长使用寿命,或者调整生产流程以适应设备性能的变化。
惠州智慧园区通过实施预测性维护方案,显著降低了设备故障率,减少了非计划停机时间,提高了生产线的稳定性和生产效率。此外,该方案还促进了资源的优化配置,降低了总体运营成本,增强了企业的市场竞争力。
惠州智慧园区内智慧工厂的实践表明,通过引入预测性维护技术,企业能够实现设备状态的精细化管理,有效减少故障风险,提升生产效率和产品质量。这种基于数据驱动的维护策略不仅能够为企业带来直接的经济效益,还推动了制造业向更加智能、可持续的方向发展。未来,随着技术的不断进步和应用场景的拓展,预测性维护将在更多领域展现出其巨大的潜力和价值。
Copyright © 2002-2024